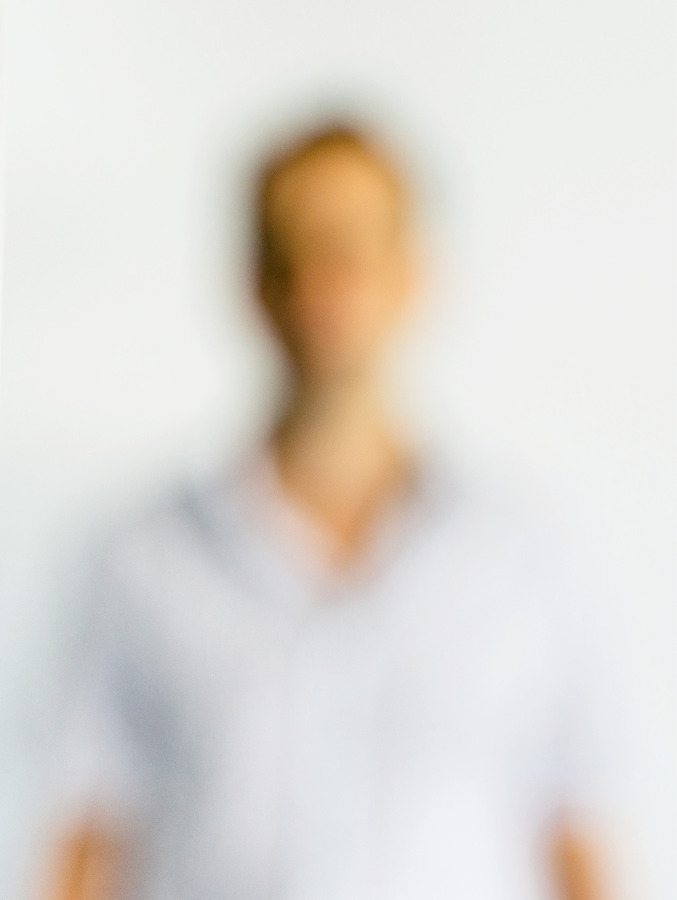
Florian Butollo
„Es wird genügend anspruchsvolle Tätigkeiten geben“
Wie verändert sich die Fabrikarbeit? Antworten von Florian Butollo, Industriesoziologe am Berliner Weizenbaum-Institut für die vernetzte Gesellschaft.
Sie haben bereits ein brand eins Konto?
Melden Sie sich hier an.
Wir freuen uns, dass Ihnen dieser Artikel gefällt.
Zum Weiterlesen wählen Sie eine dieser Optionen
Wir freuen uns, dass Ihnen dieser Artikel gefällt.
Er ist Teil unserer Ausgabe Personal
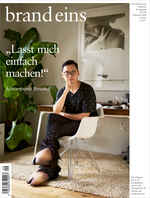
Sicher bezahlen mit
Weitere Abos, Schüler- & Studentenrabatte